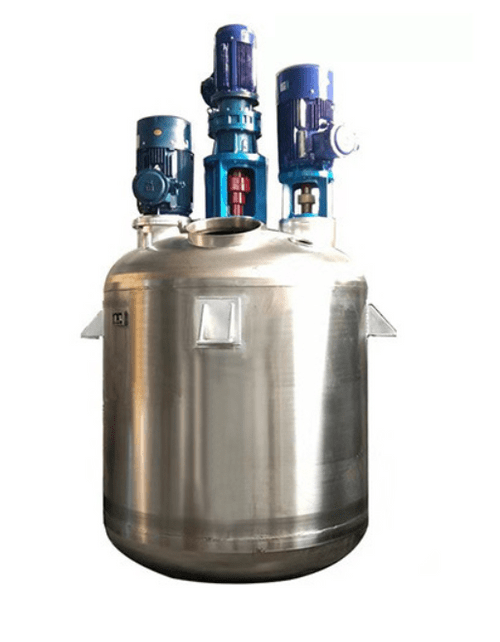
Three shafts mixing reactor
1. Introduction:
The reaction kettle has the characteristics of rapid heating, high temperature resistance, corrosion resistance, no environmental pollution, etc. It is widely used in petroleum, chemical, rubber, pesticide, dye, medicine, food and other industries. It is also used to complete vulcanization, nitration, hydrogenation, alkylation, Processes such as condensation and polymerization.
2. The materials of the reactor are generally carbon-manganese steel, stainless steel, zirconium, nickel-based (Hastelloy, Monel, Inconel) alloys and other composite materials; according to the manufacturing structure of the reactor, it can be divided into open-type flat-cover reactors , open butt welding flange reaction kettle and closed reaction kettle three categories, each structure has its scope of application and advantages and disadvantages.
3. According to the different sealing types of the reactor, it can be divided into: packing seal, mechanical seal and magnetic seal.
4. The reaction kettle is composed of a kettle body, a kettle cover, a jacket, a stirrer, a transmission device, a shaft sealing device, and a support. The stirring forms generally include anchor type, paddle type, turbine type, propulsion type or frame type, etc. When the height-diameter ratio of the stirring device is large, multi-layer stirring blades can be used, and it can also be selected according to the user's requirements. A jacket is set outside the kettle wall, or a heat exchange surface is set inside the vessel, or heat exchange can be carried out through external circulation.
5. The heating methods include electric heating, hot water heating, heat transfer oil circulating heating, far-infrared heating, outer (inner) coil heating, etc. The cooling methods are jacket cooling and inner coil cooling in the kettle, and the form of stirring paddles, etc.
6. The support base has support type or ear type support, etc. Gear reducers should be used when the speed exceeds 160 rpm. The number of holes, specifications or other requirements can be designed and manufactured according to user requirements.
7.Example for tile gap caulking filler glue formula:
The formula includes component A and component B; in parts by weight, the raw materials of component A include 90-128 parts of epoxy resin, 2-10 parts of fumed silica, and 1-3 parts of bactericide; In parts by weight, the raw materials of component B include 18-34 parts of curing agent, 0.5-1 part of lignosulfonate, 0.5-1 part of polyoxyethylene ether, 15-27 parts of benzyl alcohol, and 3-10 parts of pigment. parts, and 8-15 parts of inorganic fillers.