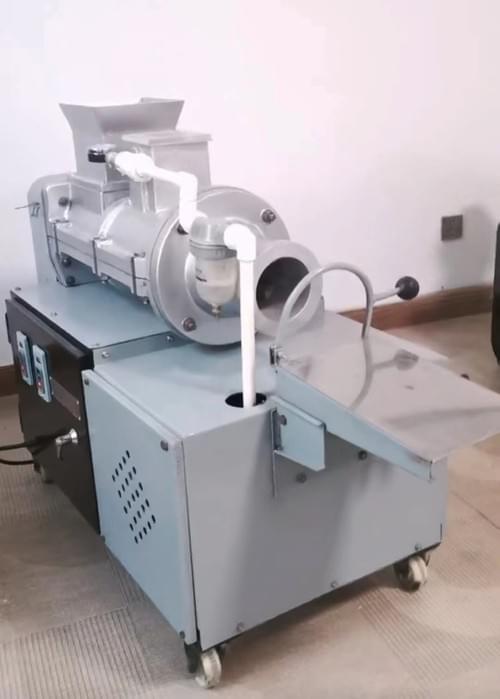
110mm easy cleaning vacuum de-airing pottery ceramic pocerlain pugmill with aluminum barrel
Pottery contacting parts are SS304 (aluminum barrel).
With a motor of 2.2KW.
With a 0.55kw vacuum pump.
Two-shaft feeding,two- shaft discharging.
Fast open and easy cleaning type.
1. Working principle of pottery pugmill:
The clay is put into the double-shaft screw mixing chamber from the feeding port. The clay is first broken by the discontinuous blades, kneaded, and then pushed forward. After the screening plate, the surface area of the clay is enlarged, and the internal gas is gradually passed through vacuum pump suction to remove. The clay continues to move forward while degassing, and the gas has basically been discharged when it reaches the vacuum chamber. Finally, the clay is extruded from the extrusion port, and then it is cut into the required size through the working platform.
2.Main structure:
1) Transmission part: motor, reducer, chain, etc.;
2) Feeding port, pressing device and stainless steel storage table;
3) Mud mixing part (first stage): horizontal double shaft feeding design.
The main components are two pieces of discontinuous propeller blades. The function is: crushing, mixing and conveying the mud.
4) Vacuum chamber and auxiliary parts: including vacuum pump, shock-proof vacuum meter, water vapor absorption bottle, etc.
Note: The mud itself will form a seal against the vacuum chamber. If the vacuum chamber is full, it must be cleaned in time.
5) Mud extrusion part (second stage): The vacuum degassed mud is conveyed and extruded to eliminate the spiral structure and finally sent out the extrusion port (it also forms a seal to the vacuum chamber). The main components are: the helical structure of the continuous blade.
3.Technical parameter:
1. Motor power: 1.1KW;
2. Equipped with rotary vane vacuum pump: 0.55KW;
3. Output: about 400-500 kg/hour;
4. Suitable for 220V, 50HZ, single-phase or customized.
5. Double-shaft stainless steel spiral blade for feeding, single-spiral for discharging.
6. Extruder port diameter: 80mm or customized.
7. Dimensions: L: 1300*W: 400*H: 800mm.
8. Weight: 176kg.
4.Details: